Tapware of Laveo quality
Attractive design and high quality are essential components of all collections of tapware we create at Laveo. We take care of high standards of our products which find their place in bathrooms and kitchens of our customers at each stage of the journey taken by a series – from design, through production, to warranty and post-warranty service.
Let us present QUALITY under Laveo brand.
From idea to accomplishment or how tapware is created
Preparation of a new model or the whole series of tapware at Laveo is preceded by an in-depth market analysis and observation of customers’ habits and ever-changing trends. Throughout more than 10 years of our presence on the Polish and foreign markets we have gained valuable experience which translates to successful designs, proven by the sales results.Product Managers, who gain their professional experience on a widely understood designers’ market, are responsible for the design of a mixer or a shower. All of them in their work exceed by far the limits of their entrusted area and take inspirations among others from architecture, fashion world, or arts. Each of product groups is taken care of by a single person, specialized in a specific field. However, at a stage of developing of a new collection, they all work as a team to make sure that each mixer, column or hand shower will be fully functional and will find a complementation in other products available in the brand portfolio.
Designs of new models are created in a close cooperation with technologists employed in the related factories. With this we have a guarantee that our products combine attractive form and optimum ergonomics within, and meet all standards required by Polish and Community legislation.
Apart from that bathroom and kitchen tapware by Laveo have attestation of the National Institute of Public Health which is a guarantee of hygienic safety. Products covered by hygienic attestation can be connected to systems used to transport water intended for human consumption. They can be mounted in both residential and public utility buildings – including educational and day-care, healthcare facilities, and service and industrial establishments.
The first stage of production of a new model is preparation of a prototype. The first version is created with use of a 3D printer. At this stage we assess whether a design actually meets preliminary assumptions, in terms of comfort of use, in particular.
The second stage is preparation of a product 1:1 with use of target components, production methods and finish application techniques. Once a sample is accepted, the actual production is launched.
Components and production methods
Tapware by Laveo in the vast majority is made of brass. This is a special material thanks to its properties. First, it is resistant to corrosion, which is particularly relevant in case of sanitary products that have a constant contact with water. Second, brass is safe – it does not cause precipitation of any substances that are harmful to human health. Third, its huge advantage is plasticity, and thus in the production process we can give it any shape which in turn results in interesting design collections.
Apart from brass in production of tapware by Laveo, we use stainless steel 304, regarded as the most resistant and hygienic material. Stainless steel 304 is used to produce elements of wall-mounted mixers which are the most exposed to corrosion: seat and offset union.
Bona series of kitchen mixers which are made completely of stainless steel 304 is an exceptional example of the use of this material.
In some shower models smaller elements and components, for which, apart from resistance, low weight is equally relevant, are made of ABS (acrylonitrile butadiene styrene). This plastic is characterized by high rigidity and resistance to scratches, which is important, for example with hand shower brackets due to high frequency of use.
The most important part of any mixer is cartridge which as well can be called its heart. Alike the organ in human body, the cartridge is responsible for longevity and correct functioning of the mixer. All models of mixers and showers by Laveo include cartridges supplied by the internationally recognised Spanish company – Quore that is appreciated by global manufacturers of tapware.
In many series ceramic function switches are mounted which are characterized by exceptional resistance and low susceptibility to damage. Their additional advantage is comfort of use as their operation is not dependant on water pressure.
According to the desired type of finish to achieve, tapware series are subject to one of four processes. Each of them ensures the highest resistance of a particular colour and has been refined in every detail.
Electroplating. With use of this method chrome and graphite finishes are achieved, among others. It involves application of thin metallic coatings by depositing one metal on the other in electroplating bath with use of electrochemical phenomena. Such applied layer permanently adheres to the base.
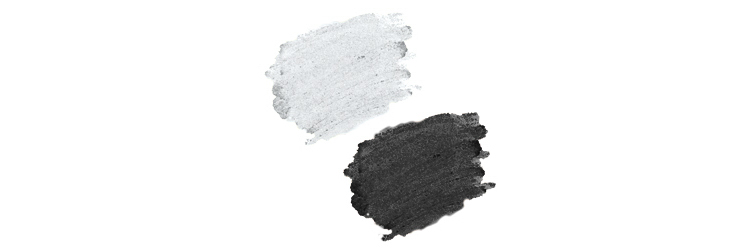
Powder coating. Used to achieve matt finishes – e.g. black and white. It involves application of electrified particles of powder paint on the base through spraying at a suitable pressure, and then soaking until cured.
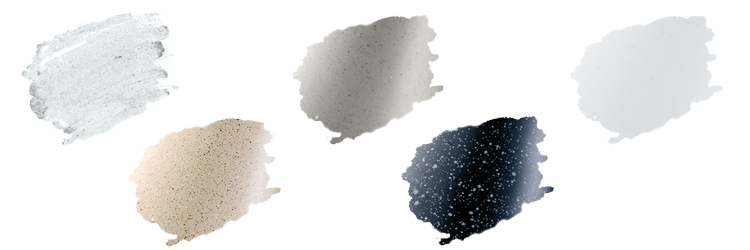
Wet painting. Allows to obtain a glossy colour, e.g. white, or granite-like finishes. It is carried out with use of liquid paint which is applied under pressure with a spray gun.
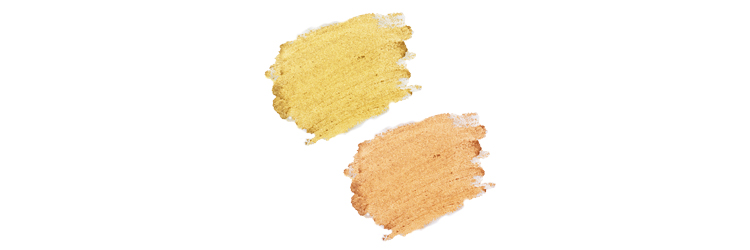
PVD technology. The so-called colour padding is used to obtain metallic shades, including yellow and rose gold. Colour application is carried out in vacuum in the process of physical vapour deposition which guarantees increased colour fastness.
Quality control
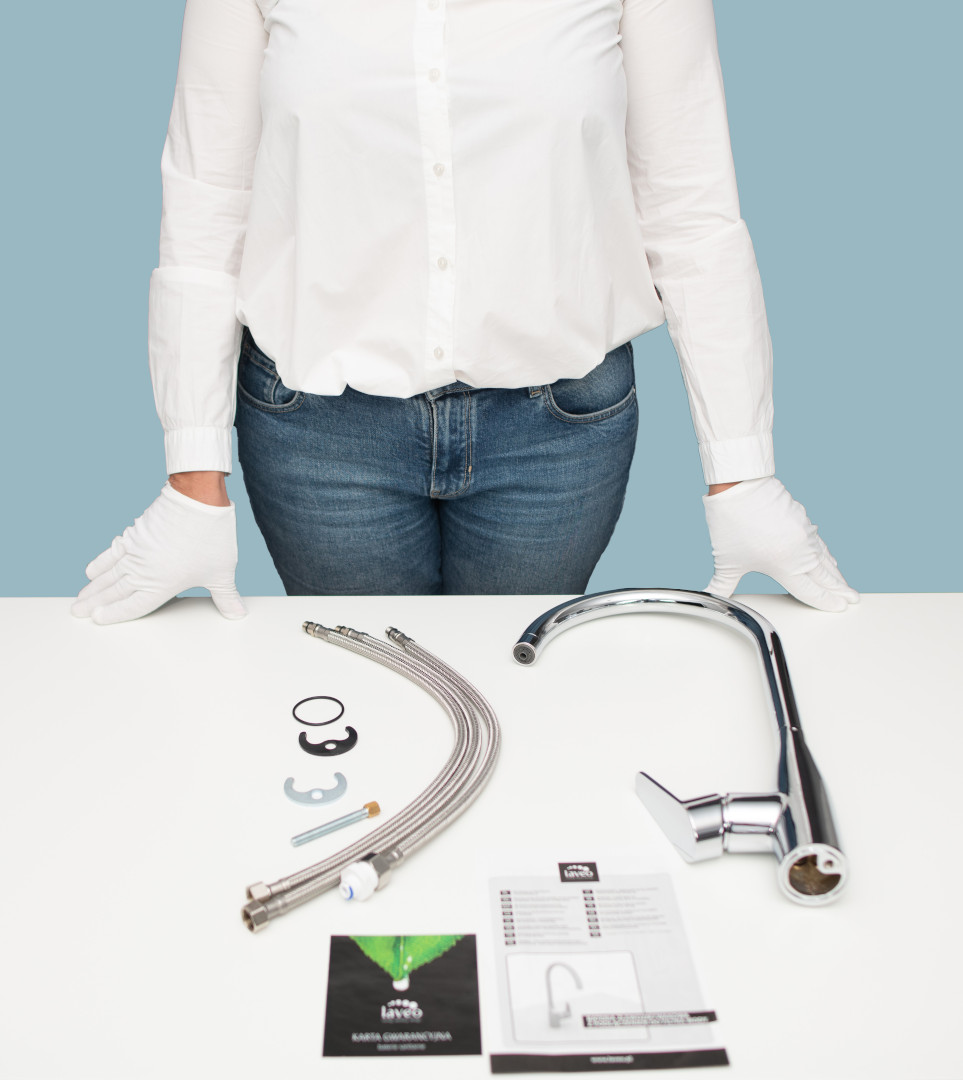
All mixers, columns and shower sets in Laveo offer are subject to a two-stage quality control. The first is carried out in production facilities we cooperate with. The other is performed at Laveo warehouse by an experienced team of inspectors gathering employees with many years of practice, knowing every detail of any product.
Quality control of each model is carried out on a basis of a chart, developed by the Product Managers Department, which contains detailed information on the product itself, additional equipment as well as system identification.
All supplies that arrive at Laveo central warehouse are subject to quality control. According to the internal procedure about 10% of randomly selected products from each batch are sent to an appropriate department.
Internal standards at Laveo define optimum conditions for performing controls of particular products, including minimum observation time, type and intensity of lighting, water and air pressure in a specialist tester and division to specific areas of surface subject to control. The procedures in a very precise way specify acceptance criteria in each part of the control being conducted, according to which tapware is qualified to appropriate grade classes.
Stages of quality control
» Label test. At first the check covers label legibility and correctness of the data contained, which is particularly important for Laveo warehouse systems and our business customers.
» Completeness test. Inspectors verify if a unit package contains all necessary elements: complete product, assembly parts and instructions.
» Assembly test. A quality control employee carries out assembly of the product and checks if a correct installation using elements supplied in the set, is possible.
» Surface test. A product is carefully tested for any possible damages: scratches, chips and discolourations. A separate control involves inspection of five areas – both sides of a product, top, front and bottom view.
» Tightness test. Carried out with a professional tester which allows to perform tightness testing with use of water and air. Tightness of the body and aerator in each model is checked in two ways.
Tester
Tapware tightness control is carried out with use of a modern, fully automated appliance controlled by experienced operators.
The tester works in two ways – with use of water in closed circuit and compressed air.
Quality of products involves not only due workmanship with use of high-quality materials. It is also a reliable service assistance and a top-level customer service.
Satisfaction and pleasure of our customers is key for us. Thus we strive to make our products meet expectations regarding both design and quality of workmanship. We also care that our website contains complete information on whole product groups and particular models. Marcin Szymke - Head of Product Managers Department |
![]() |
Central Service is available to users of Laveo products. It is located in a direct vicinity of the warehouse, and thus it can quickly respond to even those unusual requests.
From the customer’s perspective, the quickest and most comfortable contact method which allows to shorten request processing time is an on-line complaint form available at our website. The biggest advantage of this solution is a possibility to complete the form at any time using a smartphone, tablet or laptop. This also guarantees that the request submitted in such way will be sent directly to the responsible department, and thus a reply will be received sooner. Questionnaire – apart from a literal description of difficulties encountered by user – gives possibility to add photos as attachments to significantly facilitate the investigation process.
Direct contact with Laveo Service is also possible via e-mail or by telephone in the office working hours.
SERVICE LAVEOThe Service employees will reply to all questions and clear any doubts concerning functioning, assembly of products and minor maintenance works which users should carry out on their own.
In addition, they will help to select suitable spare parts.
The Service also take care of a comprehensive handling of the complaint process. They receive direct requests from individual customers and requests sent through retail stores and sales showrooms.
Most of products available in Laveo offer is covered by nation-wide service at customer’s location. Contact with a local Service Technician can be found under the following tab >> Service >> Post-warranty service.
To confirm the high quality of tapware by Laveo we should mention 8 years* warranty period and awards given to our products in prestigious competitions. Industry awards given by journalists in connection with the widely understood interior design market, architects, distributors and manufacturers, not only prove an attractive design but also the high quality.
*warranty details can be found in warranty cards of particular models.
*szczegóły gwarancji znajdują się w kartach gwarancyjnych poszczególnych modeli.